Open Access
ARTICLE
Simulation of Elastic and Fatigue Properties of Epoxy/SiO2 Particle Composites through Molecular Dynamics
Hubei Key Laboratory of Theory and Application of Advanced Materials Mechanics, School of Science, Wuhan University of Technology, Wuhan, 430070, China
* Corresponding Author: Yong Lv. Email:
(This article belongs to the Special Issue: Modeling of Heterogeneous Materials)
Computer Modeling in Engineering & Sciences 2021, 128(1), 339-357. https://doi.org/10.32604/cmes.2021.015388
Received 15 December 2020; Accepted 08 April 2021; Issue published 28 June 2021
Abstract
The influence of different nanoparticle sizes on the elastic modulus and the fatigue properties of epoxy/SiO2 nanocomposite is studied in this paper. Here, the cross-linked epoxy resins formed by the combination of DGEBA and 1,3-phenylenediamine are used as the matrix phase, and spherical SiO2 particles are used as the reinforcement phase. In order to simulate the elastic modulus and long-term performance of the composite material at room temperature, the simulated temperature is set to 298 K and the mass fraction of SiO2 particles is set to 28.9%. The applied strain rate is 109/s during the simulation of the elastic modulus. The results show that the elastic modulus of the material increases with the increase in particle size. Furthermore, fatigue simulation under strain control is performed on the model with SiO2 nanoparticle radius of 12 Å. The results indicate that the influence trend of variable frequencies on the fatigue mechanical response is similar, and the mean stress decreases with the increase in number of cycles. In addition, the smaller the loading period and the more the number of cycles, the greater the mean stress reduction. Finally, the change in energy and free volume fraction are evaluated under fatigue loading condition.Keywords
Cite This Article
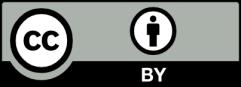
This work is licensed under a Creative Commons Attribution 4.0 International License , which permits unrestricted use, distribution, and reproduction in any medium, provided the original work is properly cited.