Open Access
ARTICLE
Impacts of Disk Rock Sample Geometric Dimensions on Shear Fracture Behavior in a Punch Shear Test
School of Highway, Chang’an University, Xi’an, 710064, China
* Corresponding Author: Tantan Zhu. Email:
(This article belongs to the Special Issue: Modeling and Simulation of Fluid flows in Fractured Porous Media: Current Trends and Prospects)
Computer Modeling in Engineering & Sciences 2021, 126(2), 457-477. https://doi.org/10.32604/cmes.2021.014284
Received 15 September 2020; Accepted 03 December 2020; Issue published 21 January 2021
Abstract
Punch shear tests have been widely used to determine rock shear mechanical properties but without a standard sample geometric dimension suggestion. To investigate the impacts of sample geometric dimensions on shear behaviors in a punch shear test, simulations using Particle Flow Code were carried out. The effects of three geometric dimensions (i.e., disk diameter, ratio of shear surface diameter to disk diameter, and ratio of disk height to shear surface diameter) were discussed. Variations of shear strength, shear stiffness, and shear dilatancy angles were studied, and the fracture processes and patterns of samples were investigated. Then, normal stress on the shear surface during test was analyzed and a suggested disk geometric dimension was given. Simulation results show that when the ratio of the shear surface diameter to the disk diameter and the ratio of disk height to the shear surface diameter is small enough, the shear strength, shear stiffness, and shear dilatancy angles are extremely sensitive to the three geometric parameters. If the ratio of surface diameter to disk diameter is too large or the ratio of disk height to surface diameter is too small, a part of the sample within the shear surface will fail due to macro tensile cracks, which is characterized by break off. Samples with a greater ratio of disk height to shear surface diameter, namely when the sample is relatively thick, crack from one end to the other while others crack from both ends towards the middle. During test, the actual normal stress on the shear surface is greater than the target value because of the extra compressive stress from the part of sample outside shear surface.Keywords
Cite This Article
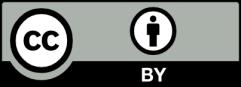
This work is licensed under a Creative Commons Attribution 4.0 International License , which permits unrestricted use, distribution, and reproduction in any medium, provided the original work is properly cited.