Open Access
ARTICLE
Mesoscopic-Scale Numerical Investigation Including the Inuence of Process Parameters on LPBF Multi-Layer Multi-Path Formation
Institute for Systems Rheology, School of Mechanical and Electrical Engineering, Guangzhou University, Guangzhou Higher Education Mega Center, Guangzhou, 510006, China
* Corresponding Author: Liu Cao. Email:
(This article belongs to the Special Issue: Design & simulation in Additive Manufacturing)
Computer Modeling in Engineering & Sciences 2021, 126(1), 5-23. https://doi.org/10.32604/cmes.2021.014693
Received 20 October 2020; Accepted 19 November 2020; Issue published 22 December 2020
Abstract
As a typical laser additive manufacturing technology, laser powder bed fusion (LPBF) has achieved demonstration applications in aerospace, biomedical and other fields. However, how to select process parameters quickly and reasonably is still the main concern of LPBF production. In order to quantitatively analyze the inuence of different process parameters (laser power, scanning speed, hatch space and layer thickness) on the LPBF process, the multi-layer and multi-path forming process of LPBF was predicted based on the open-source discrete element method framework Yade and the open-source finite volume method framework OpenFOAM. Based on the design of experiments method, a four-factor three-level orthogonal test scheme was designed, and the porosity and surface roughness data of each calculation scheme were extracted. By analyzing the orthogonal test data, it was found that as the laser power increased, the porosity decreased, and as the scanning speed, hatch space, and layer thickness increased, the porosity increased. In addition, the inuence of laser power and scanning speed on surface roughness showed a trend of decreasing first and then increasing, while the inuence of scanning distance and layer thickness on surface roughness showed a monotonous increasing trend. The order of the inuence of each process parameter on porosity was: scanning speed > laying thickness > laser power > hatch space, and the order of the inuence of each process parameter on surface roughness was: hatch space > layer thickness > laser power > scanning speed. So the porosity of the part is most sensitive to scanning speed, and the surface roughness is the most sensitive to hatch space. The above conclusions are expected to provide process control basis for actual LPBF production of the 316L stainless steel alloy.Keywords
Cite This Article
Citations
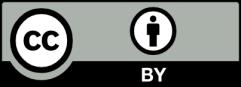
This work is licensed under a Creative Commons Attribution 4.0 International License , which permits unrestricted use, distribution, and reproduction in any medium, provided the original work is properly cited.