Open Access
ARTICLE
A New Finite Element Model with Manufactured Error for Additive Manufacturing
1 National Enterprise Information Software Engineering Research Center, School of Mechanical Science and Engineering, Huazhong University of Science and Technology, Wuhan, 430074, China
2 National Engineering Research Center of Novel Equipment for Polymer Processing, The Key Laboratory of Polymer Processing Engineering of the Ministry of Education (South China University of Technology), Guangdong Provincial Key Laboratory of Technique and Equipment for Macromolecular Advanced Manufacturing, South China University of Technology, Guangzhou, 510641, China
* Corresponding Author: Yingjun Wang. Email:
(This article belongs to the Special Issue: Design & simulation in Additive Manufacturing)
Computer Modeling in Engineering & Sciences 2020, 124(2), 703-720. https://doi.org/10.32604/cmes.2020.010368
Received 27 February 2020; Accepted 07 April 2020; Issue published 20 July 2020
Abstract
Additive manufacturing (AM), adding materials layer by layer, can be used to produce objects of almost any shape or geometry. However, AM techniques cannot accurately build parts with large overhangs, especially for the large features close to horizontal, hanging over the void. The overhangs will make the manufactured model deviate from the design model, which will result in the performance of the manufactured model that cannot satisfy the design requirements. In this paper, we will propose a new finite element (FE) analysis model that includes the manufacturing errors by mimicking the AM layer by layer construction process. In such FE model, an overhang coefficient is introduced to each FE, which is defined by the support elements in the lower layer. By mimicking the AM process from the bottom layer to the top layer, all the FE properties are updated based on their overhang coefficients, which makes the computational model be able to predict the manufactured model with manufacturing errors. The proposed model can be used to predict the performance of the AM objects in the design stage, which will help the designers to improve their design by the simulation results.Keywords
Cite This Article
Citations
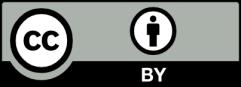
This work is licensed under a Creative Commons Attribution 4.0 International License , which permits unrestricted use, distribution, and reproduction in any medium, provided the original work is properly cited.