Open Access
ARTICLE
Investigation into Spatter Particles and Their Effect on the Formation Quality During Selective Laser Melting Processes
1 Science and Technology on Plasma Dynamics Laboratory, Air Force Engineering University, Xi’an, 710038, China
2 School of Mechanical and Automotive Engineering, South China University of Technology, Guangzhou, 510640, China
3 Aero-Space Engine & Smart Manufacturing Institute, Xi’an, 710038, China
* Corresponding Author: Xin Zhou. Email:
(This article belongs to the Special Issue: Design & simulation in Additive Manufacturing)
Computer Modeling in Engineering & Sciences 2020, 124(1), 243-263. https://doi.org/10.32604/cmes.2020.09934
Received 03 February 2020; Accepted 25 March 2020; Issue published 19 June 2020
Abstract
During the selective laser melting process, a high-energy laser beam acts on the powder, a molten pool is rapidly generated and the characteristic parameters are constantly changing. Among them, temperature is one of the important parameters in the forming process. Due to the generation of splash particles, there will be defects in the microstructure, which will seriously affect the formation quality of the prepared parts. Therefore, it is necessary to study the relationships between the splash behavior, molten pool characteristics and product quality. The finite element simulation of the transient temperature field was performed by ANSYS software. Time-series images at different frame rates were obtained with a high-speed camera, and the dynamic process of splashing was observed. Using IN718 alloy powder, the influence of the laser energy density on the light intensity of the molten pool was studied. The appearance of splash particles and the deviation of the powder chemical elements caused by the splash were analyzed. The results show that the transient temperature field with drastic change is easy to cause spatter, which is consistent with the experimental results. There are large differences in the splash at different shooting frame rates. Increasing the frame rate can allow the observation of details such as the shape, size and number of splash particles, which is beneficial for studying the process of splash formation. At the moment when the splash occurs, the light intensity of the molten pool always first increases and then decreases, depending on the energy input. The higher the energy input is, the more intense the light intensity of the molten pool and the higher the peak interval distribution. Compared with fresh powder, the contents of Al and Ti in powder reused 5 times were reduced by 0.15% and 0.02%, respectively. The increases of these two elements in the splash were 16.18% and 29.62%, respectively, and the content of Nb even exceeded the standard range. When the energy density decreased from 229.17 J/mm3 to 130.95 J/mm3 , the relative density of the part increased from 91.82% to 99.83%. This shows that reducing the energy input can reduce the splash to suppress the generation of defects, along with the weakening of the overall light intensity of the molten pool. These results can provide a basis for feature extraction of the molten pool, which is of great significance for real-time monitoring and online control in manufacturing processes and ensuring product quality.Keywords
Cite This Article
Citations
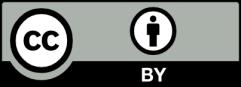
This work is licensed under a Creative Commons Attribution 4.0 International License , which permits unrestricted use, distribution, and reproduction in any medium, provided the original work is properly cited.