Open Access
ARTICLE
Numerical Simulation and Experimental Studies on Elastic-Plastic Fatigue Crack Growth
School of Mechanical Engineering, Dalian University of Technology, Dalian, 116024, China .
* Corresponding Author: Wei Jiang. Email: .
Computer Modeling in Engineering & Sciences 2019, 118(2), 377-395. https://doi.org/10.31614/cmes.2019.01836
Abstract
A elastic-plastic fatigue crack growth (FCG) finite element model was developed for predicting crack growth rate under cyclic load. The propagation criterion for this model was established based on plastically dissipated energy. The crack growth simulation under cyclic computation was implemented through the ABAQUS scripting interface. The predictions of this model are in good agreement with the results of crack propagation experiment of compact tension specimen made of 304 stainless steel. Based on the proposed model, the single peak overload retardation effect of elastic-plastic fatigue crack was analyzed. The results shows that the single peak overload will reduce the accumulation rate of plastic energy dissipation of elements at crack tip plastic zone, so that crack growth will be arrested. The crack growth rate will not recover until the crack tip exceed the affected region. Meanwhile, the crack growth rate is mainly determined by the amplitude rather than the mean load under the condition of small scale yielding. The proposed model would be helpful for predicting the growth rate of mode I elastic-plastic fatigue crack.Keywords
Cite This Article
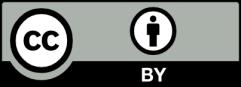
This work is licensed under a Creative Commons Attribution 4.0 International License , which permits unrestricted use, distribution, and reproduction in any medium, provided the original work is properly cited.