Open Access
ARTICLE
Model of CEL for 3D Elements in PDMs of Unidirectional Composite Structures
Beijing Key Laboratory of Civil Aircraft Structures and Composite Materials, BASTRI of COMAC, Beijing, 102211, China.
School of Astronautics, Beihang University, Beijing, 100191, China.
Key Laboratory of Spacecraft Design Optimization and Dynamic Simulation Technologies, Minisitry of Education, Beihang University, Beijing 100191, China.
State Key Laboratory for Strength and Vibration of Mechanical Structures, Xi'an Jiaotong University, Xi'an 710049, China.
College of Aerospace Engineering, Chongqing University, Chongqing, 400044, China.
* Corresponding Author: Libin Zhao. Email: .
Computer Modeling in Engineering & Sciences 2019, 118(1), 157-176. https://doi.org/10.31614/cmes.2019.04379
Abstract
Progressive damage models (PDMs) have been increasingly used to simulate the failure process of composite material structures. To accurately simulate the damage in each ply, 3D PDMs of composite materials have received more attention recently. A characteristic element length (CEL), which is an important dimensional parameter of PDMs for composite materials, is quite difficult to obtain for 3D elements, especially considering the crack directions during damage propagation. In this paper, CEL models for 3D elements in PDMs of unidirectional composite structures are presented, and their approximate formulae are deduced. The damage in unidirectional composite materials can be divided into fiber cracks and inter-fiber cracks. The fiber crack and inter-fiber crack directions are considered in the CEL derivations, and thus, the CELs of 3D elements that have various damage modes and damage directions could be obtained relatively precisely. Static tensile and compressive tests of open-hole laminates were conducted, and the corresponding numerical analyses by the progressive damage method, including the proposed CEL models and those models from the literature, were performed. The numerical results are in good agreement with the experimental results, which proves the fidelity and effectiveness of the proposed CEL models. In addition, the proposed CEL models have better performance in improving the mesh independence of the numerical models.Keywords
Cite This Article
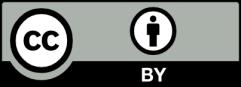
This work is licensed under a Creative Commons Attribution 4.0 International License , which permits unrestricted use, distribution, and reproduction in any medium, provided the original work is properly cited.