Open Access
ARTICLE
Progressive Failure Evaluation of Composite Skin-Stiffener Joints Using Node to Surface Interactions and CZM
Department of Mechanical Engineering, Visvesvaraya National Institute of Technology, Nagpur, 440010, India.
*Corresponding Author: A. Sane. Email: .
Computer Modeling in Engineering & Sciences 2018, 115(2), 281-294. https://doi.org/10.3970/cmes.2018.05046
Abstract
T shaped skin-stiffener joint are one of the most commonly used structures in aerospace components. It has been proven in various studies that these joints are susceptible to failure when loaded in pull out conditions however, in specific applications these joints undergo pull loading. De-lamination/de-bond nucleation and its growth is one of the most common failure mechanisms in a fiber reinforced composite structure. Crack growth takes place due to the induced interlaminar normal and shear stresses between different structural constituents when a load is applied. In this study, Finite Element Analysis has been performed using cohesive contact interactions on a composite T-joint to simulate the pull out test conditions. A simplified shell based model coupled with CZM is proposed, which can evaluate the failure initiation and progression accurately with lesser computational efforts. The final failure occurred at a displacement of 4.71 mm at the computed failure load of 472.57 kgf for basic configuration. Computed Failure load for the padded configuration is 672.8 kgf and corresponding displacement is 4.6 mm. The results obtained by the proposed numerical model are validated by experimental results and it is observed that predicted failure displacements and failure load calculated were correlating reasonably well with the experiment.Keywords
Cite This Article
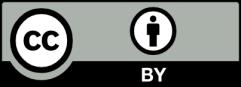
This work is licensed under a Creative Commons Attribution 4.0 International License , which permits unrestricted use, distribution, and reproduction in any medium, provided the original work is properly cited.