Open Access
ARTICLE
Simulation of Hot Shape Rolling of Steel in Continuous Rolling Mill by Local Radial Basis Function Collocation Method
University of Nova Gorica, Nova Gorica, Slovenia.
IMT, Ljubljana, Slovenia.
Corresponding author: Professor Božidar Šarler. E-mail: bozidar.sarler@imt.si; bozidar.sarler@ung.si
Computer Modeling in Engineering & Sciences 2015, 109-110(5), 447-479. https://doi.org/10.3970/cmes.2015.109.447
Abstract
The aim of this paper is to demonstrate the use of the novel Local Radial Basis Function Collocation Method (LRBFCM) [Šarler and Vertnik (2006)] in an industrial coupled thermo-mechanical problem of hot shape rolling of steel. The physical concept of such a large deformation problem is based on a two dimensional traveling slice model [Glowacki (2005)], which assumes deformation and heat flow only in the perpendicular direction to rolling. The solution is performed based on strong formulation. Elliptic Node Generation (ENG) is applied to reposition the nodes over a slice when necessary in order to sustain stability throughout the simulation. Coupled mechanical equilibrium steady Navier-Cauchy equations for a quasi-elastic material with temperature dependent material properties and the transient heat conduction equations are considered. The displacement and traction boundary conditions are assumed in the mechanical model and Dirichlet and Neumann boundary conditions in the thermal model, both specific for hot shape rolling. The solution procedure for mechanical model is based on local collocation on seven nodded influence domains with multiquadrics radial basis functions, augmented with the first order polynomials. Five nodded subdomains and explicit time-stepping are used in the thermal model. The elements of the thermomechanical LRBFCM model are tested on 3 different test cases: bending of a cantilever beam, compression and convective cooling. The results are compared with either FEM or analytical solution. The LRBFCM results of hot shape rolling of steel for a continuous 5 stand rolling mill are presented for the case of rolling of a rectangular billet from initial dimension 80 mm x 95 mm to a circular bar with a diameter of 60 mm. The advantage of the meshless method is in accuracy and straightforward node generation that does not require any polygonisation. The paper presents one of the increasingly emerging examples of the industrial use of LRBFCM.Keywords
Cite This Article
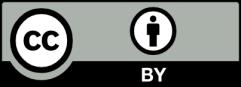
This work is licensed under a Creative Commons Attribution 4.0 International License , which permits unrestricted use, distribution, and reproduction in any medium, provided the original work is properly cited.